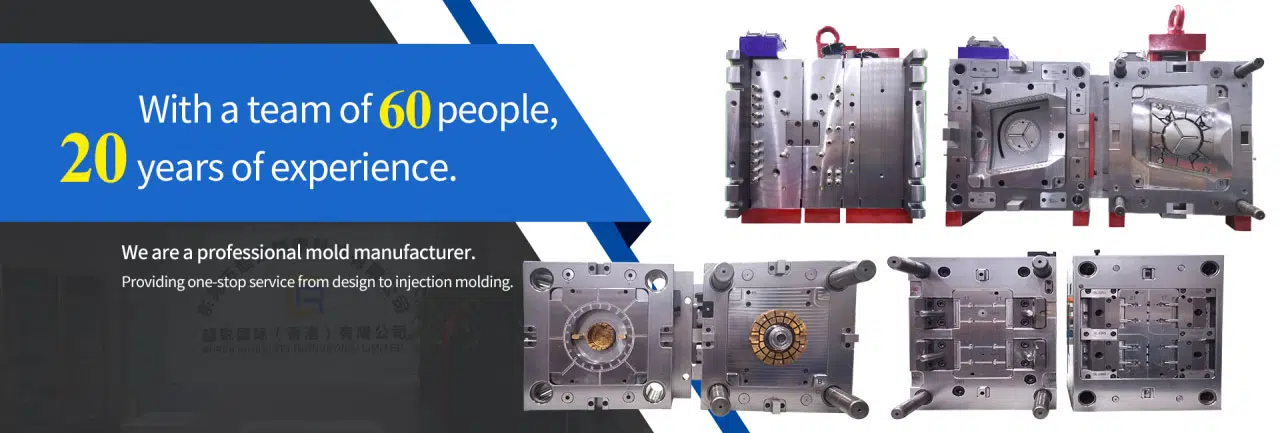
,文章长度在1000字左右。
# Sand Casting Process Overview
Sand casting is one of the oldest and most widely used metal casting processes. It involves pouring molten metal into a sand mold cavity, allowing it to solidify, and then breaking away the sand mold to reveal the finished casting. This process is versatile, cost-effective, and suitable for both small and large-scale production.
## History of Sand Casting
The origins of sand casting can be traced back thousands of years to ancient civilizations. Early metalworkers discovered that packing moist sand around a pattern could create a mold capable of holding molten metal. Over centuries, the process evolved with better sand mixtures, improved pattern-making techniques, and more sophisticated metal pouring methods.
Keyword: Sand Casting
## Basic Components of Sand Casting
Several key components are essential for the sand casting process:
– Pattern: A replica of the final product used to create the mold cavity
– Molding sand: Specially formulated sand that holds its shape when packed
– Flask: A rigid frame that contains the molding sand
– Core: Sand inserts that create internal cavities in the casting
– Gating system: Channels that allow molten metal to flow into the mold
## The Sand Casting Process Step-by-Step
### 1. Pattern Creation
The process begins with creating a pattern, typically made from wood, metal, or plastic. The pattern must account for shrinkage and include necessary draft angles for easy removal from the sand.
### 2. Mold Preparation
Molding sand is packed around the pattern within the flask. The sand mixture typically contains:
– 85-95% silica sand
– 5-10% clay (usually bentonite)
– 2-5% water
– Possible additives like coal dust or sea coal
### 3. Pattern Removal
Once the sand is properly compacted, the pattern is carefully removed, leaving behind a cavity that matches the shape of the desired casting.
### 4. Core Placement (if needed)
For castings with internal features, sand cores are placed in the mold cavity before closing the mold.
### 5. Mold Assembly
The cope (top half) and drag (bottom half) of the mold are assembled, ensuring proper alignment through pins or other registration systems.
### 6. Pouring
Molten metal is poured into the mold through the gating system at the proper temperature and rate to ensure complete filling without defects.
### 7. Cooling
The casting is allowed to cool and solidify within the mold. Cooling time depends on the metal used and the casting’s thickness.
### 8. Shakeout
After sufficient cooling, the sand mold is broken apart to remove the casting. The sand can often be reclaimed and reused.
### 9. Finishing
The casting undergoes various finishing operations:
– Removal of gates and risers
– Grinding and smoothing of surfaces
– Possible heat treatment
– Final inspection and quality control
## Advantages of Sand Casting
Sand casting offers numerous benefits that contribute to its widespread use:
– Cost-effective for low to medium production quantities
– Can produce very large castings (up to several tons)
– Suitable for nearly all metal alloys
– Relatively simple tooling requirements
– Good dimensional accuracy for most applications
– Flexibility in design changes
## Common Applications
Sand casting finds applications across numerous industries:
– Automotive: Engine blocks, cylinder heads, transmission cases
– Industrial machinery: Pump housings, valves, gears
– Railroad: Wheels, couplers, brake components
– Construction: Pipe fittings, decorative elements
– Art and sculpture: Large bronze statues and installations
## Variations of Sand Casting
Several specialized sand casting methods have been developed:
– Green sand casting: Uses moist sand without baking
– Dry sand casting: Molds are baked to increase strength
– Skin-dried molds: Only the mold surface is dried
– Shell molding: Uses resin-bonded sand for higher precision
– Vac